常見問題
雙金屬復合耐磨彎頭研究生產(chǎn)
更新時間??2021-04-14 18:28 閱讀
煤粉輸送管 道是火電廠 運營過程中 的關鍵配 件,煤粉的輸送是一個快速而持續(xù)的過程,較快的 輸送速度使管道承受嚴重的沖擊磨 損, 在彎頭部 位經(jīng)常發(fā)生穿洞失效現(xiàn)象, 使用壽 命僅為直管 的 1/3,頻繁的維 修補焊已 成 為 影 響 煤 粉 輸 送 效 率 的 重 要 因 素 之 一 [1]。 目前 , 電 廠 使 用 的 彎 頭 多 為 16Mn 單一 材 質(zhì),硬 度 低,耐 磨 性 能 差。 單 位 承 接 某 電 廠 大 型 彎 頭,金 屬 焊 接 制 成,其 形 狀 如 圖 1。 為提高彎頭的使用壽命, 將單一材質(zhì) 改為雙金屬 復 合 彎 頭,彎 頭 尺 寸 較 大,為 保 證 其 品 質(zhì),采 用 消 失模鑄造工藝[2]。
1 試驗方法
復合彎頭外壁非工作層采用鋼管分節(jié)對接,內(nèi) 部工作層模型由手工電阻絲切割聚苯乙烯泡沫 而 成,涂刷水基石英粉專用耐火涂料,在烘干室內(nèi)進行干燥,選用底抽式真空砂箱;砂箱于二維振動臺進 行震動;采用中頻感應爐熔煉高鉻鑄鐵,澆注前,開 啟抽真空系統(tǒng),鐵液出爐溫度為 1 480 ℃,澆注溫度控制在 1 420~1 430 ℃,熱處理在臺車式電阻爐內(nèi) 進行, 耐磨性試驗在 NUS-IS03 型磨粒磨損試驗機 上進行。
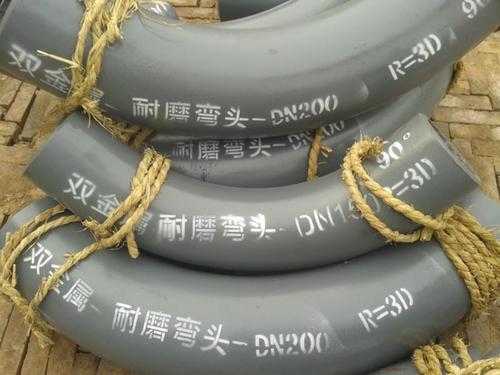
2 試制過程與結果分析
2.1 彎頭材質(zhì)成分選擇
輸送煤粉過程中,彎頭部位承受煤粉的沖擊與 磨損嚴重,因此要求彎頭具備很好的耐磨性,同時, 彎頭的安裝、拆卸、以及使用過程中的維修都要求 其具有良好的焊接性能。 在電廠工況下,高鉻鑄鐵 的抗磨損性能是最好的[1],但脆性很高,若單一使用 高鉻鑄鐵材質(zhì),彎頭不能焊接。使用 16Mn 材質(zhì)鋼管 與之復合鑄造, 不僅使彎頭具備了良好的耐磨性 能,而且實現(xiàn)了焊接,很大程度提升了彎頭的使用 周期。
試 驗 彎 頭 工 作 層 高 鉻 鑄 鐵 各 元 素 含 量 根 據(jù) GB/T8263-2010 中 BTMCr15 選定 w 為:2.0%~3.6% C;≤1.2%Si;2.0%Mn;14%~18%Cr;≤3.0%Mo;≤ 2.5%Ni;Cu≤1.2%;≤0.06%P;≤0.06%S。 彎頭外層 非工作層選用 16Mn 材質(zhì)鋼管。
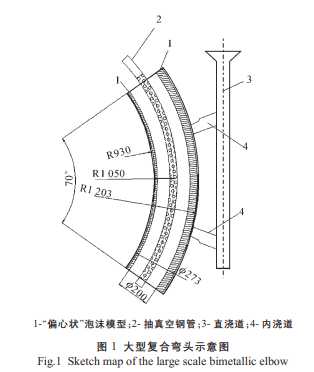
2.2 復合彎頭非工作部位制作工藝
所研 制 的 彎 頭 外 型 尺 寸 如 圖 1,中心 弧 長 為 1 282 mm,對應的半徑為 R1 050 mm,彎頭 兩端所 成中心角為 70°;采購成品 16Mn 材質(zhì)鋼管,鋼管外 徑為 準273 mm,壁厚 6 mm,用線切割的方法,將鋼 管根據(jù)所試制彎頭的角度切分為 7 段, 并按 1∶1 放 大樣進行焊接,形成彎頭的非工作部位。
2.3 工作部位模型制作工藝
工業(yè)發(fā)達國 家在開發(fā)消 失模鑄造工 藝的過程 中,重點對大型鑄件泡沫模型的熱解特性,金屬充 型凝固特性, 干砂充填緊實度等專題進行研究,并 取得了很好效果[3~6]。 因所制彎頭尺寸較大,故內(nèi)部 工作部位采用消失模鑄造工藝制備。
煤粉在輸送過程中,彎頭背部所受的沖擊磨損 最嚴重,所以內(nèi)部工作層設計采用沿弧逐漸加厚的 “偏心”結構,如圖 1 中 1 所示;彎頭內(nèi)部工作層“偏 心”狀模型的制作選用聚苯乙烯泡沫,采用電阻絲 手工切割, 鑄造收縮率為 1%。 將泡沫模型分節(jié)切 割,填充于鋼管彎頭內(nèi),并盡量做到嚴絲合縫,有縫 隙之處用報紙粘貼嚴實,填堵完成后涂刷鎂砂粉涂 料,涂層厚度約 2.0~2.5 mm。 因彎頭尺寸較大,為防 止塌箱,涂料涂刷 4 遍,每層涂刷后在烘干室內(nèi)進 行烘干,待完全干燥后涂刷下一層。
2.4 澆注系統(tǒng)設計
由于彎頭尺寸較大,采用水平式澆注易發(fā)生塌箱事故。經(jīng)試驗,澆注工藝采用如圖 1 中的豎立式階 梯澆注[7]。 階梯澆注系統(tǒng)分 2 層澆道,兩個內(nèi)澆道 向同一方向傾斜;便于補縮、同時防止鐵液冷卻收縮 將其拉裂。 根據(jù)文獻介紹[8],階梯式澆注系統(tǒng)的直 澆道 截面積應大于其他澆道截面積, 研制試驗設 計直澆道截面尺寸 45 mm×45 mm,內(nèi)澆道截面尺寸 30 mm×45 mm,長 180 mm。
2.5 模型合箱
彎頭內(nèi)涂料完全干透后, 將模型與澆注系統(tǒng)組 裝 完整,同時在 彎 頭 內(nèi) 設 置 抽 真 空 鋼 管,圖 1 中 2 所示。 之前試制過程中因沒設抽真空鋼管, 發(fā)生脹箱 和塌箱現(xiàn)象,致鑄件不合格,經(jīng)分析討論其原因為: 彎頭內(nèi)腔型砂緊密度和硬度不夠。 彎頭內(nèi)部設置抽 真空鋼管可增強型砂硬度和緊密度, 有效防止脹箱 等現(xiàn)象發(fā)生。
抽真空鋼管固定于彎頭內(nèi)中心位置, 避免偏心 與內(nèi)壁接觸,防止抽塌。將組裝好的模型整體放入砂 箱內(nèi),檢查涂料有無脫落或“露白”現(xiàn)象,若有發(fā)生及 時用泥粘嚴,避免澆注時型砂進入鑄件形成夾砂。 砂箱內(nèi)以硅砂作為型砂, 模型在砂箱內(nèi)的吃砂 量 為:下 部 90~100 mm,四壁 與 上 部 120~150 mm。 將砂箱置于二維震動臺震動 1 min 左右, 后吊入澆 注坑。 表面覆蓋塑料薄膜,放置澆口杯,將潮砂覆于 薄膜上, 用于固定澆口杯以及防止外濺鐵液燒破薄 膜而泄壓。
2.6 鐵液熔煉與澆注
高 鉻 鑄 鐵 的 熔 煉 在 250 kg 中 頻 感 應 爐 內(nèi) 進 行,按照已設定鐵液的化學成分進行配料計算。 裝 爐時爐料要緊密,以求快速熔化;開始通電 6~8 min 內(nèi)先以小功率送電,待電流沖擊停止 后,逐漸將功 率 增 至 最 大 ; 熔 煉 過 程 中 應 隨 時 推 料 防 止 “搭 橋 ” ,并 陸 續(xù) 添 加 爐 料。 待 爐 料 全 部 熔 化,溫 度 升 至 1 480 ℃時出 鐵 液, 并 開 啟 真 空 泵, 鐵 液 鎮(zhèn) 靜 2~3 min 后進行澆注。澆注完成后將負壓度調(diào)整為 -0.025 MPa,抽真空保持 15 min 關閉真空泵,鑄件 于砂箱內(nèi)保溫 8 h 倒箱。 鑄件在空氣中冷卻。
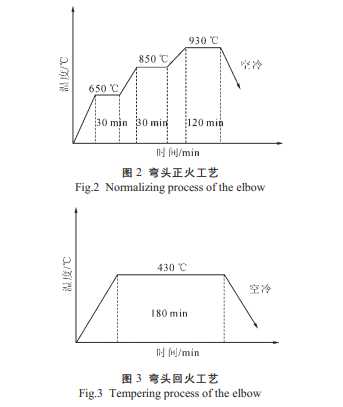
2.7 熱處理工藝
為了提高大型復合彎頭使用壽命, 達到火力發(fā) 電廠輸送煤粉的指標要求, 對彎頭進行了正火和回 火處理。 正火和回火工藝如圖 2 和圖 3 所示。
2.8 耐磨性試驗及結果分析
為對比雙金屬彎頭與單一材質(zhì) 16Mn 彎頭的耐 磨損性能, 分別從研制成功的雙金屬彎頭及 16Mn 彎頭上取樣,進行了磨粒磨損試驗。將 試樣 制 成 50 mm×50 mm×4 mm 的試 樣 塊, 于 NUS-ISO3 型磨粒磨損試驗機上進行磨損試驗, 記 錄 試 樣 減 重 量;對 試 驗 機“往 復 次 數(shù)”及 試 樣 塊 “累計減重量” 用的函數(shù)關系 Origin 軟件進行直線 擬合,分別得到如圖 4 所示的兩條直線,直線斜率 即表示試樣的磨損率。
從圖 4 中直線 斜率可以得 出: 雙 金 屬 彎 頭 試 樣 的 耐 磨 性 能 是 16Mn 材 質(zhì) 彎 頭 耐 磨 性 能 的 2.05倍。
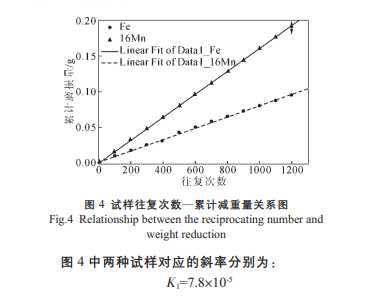
2.9 大型雙金屬彎頭的應用
研制成功的大型復合彎頭在某電廠進行了裝機 試驗,現(xiàn)場跟蹤表明:使用了 18 個月未發(fā)現(xiàn)穿孔失 效現(xiàn)象, 較該電廠原配彎頭使用壽命提高 2~3 倍, 品質(zhì)得到該電廠的認可。
3 結論
(1)采用消失模固液復合鑄造 16Mn 材質(zhì)鋼-高 鉻鑄鐵復合大型彎頭, 既保證了彎頭良好的焊接性 能,同時擁有很高的耐磨性,大幅度增加了彎頭的使 用周期,提高了煤粉輸送效率。
(2)(2)澆注 過 程 中,采 用 豎 立 式 階 梯 澆 注 并 在 復 合 彎頭內(nèi)添加抽真空鋼管,有效解決了塌 箱、脹箱 問題。
(3)(3)與單一材質(zhì) 16Mn 彎頭相比,雙金屬復合彎 頭的耐磨性能是其 2.05 倍, 使用壽命較前者提高 2~3 倍。
1 試驗方法
復合彎頭外壁非工作層采用鋼管分節(jié)對接,內(nèi) 部工作層模型由手工電阻絲切割聚苯乙烯泡沫 而 成,涂刷水基石英粉專用耐火涂料,在烘干室內(nèi)進行干燥,選用底抽式真空砂箱;砂箱于二維振動臺進 行震動;采用中頻感應爐熔煉高鉻鑄鐵,澆注前,開 啟抽真空系統(tǒng),鐵液出爐溫度為 1 480 ℃,澆注溫度控制在 1 420~1 430 ℃,熱處理在臺車式電阻爐內(nèi) 進行, 耐磨性試驗在 NUS-IS03 型磨粒磨損試驗機 上進行。
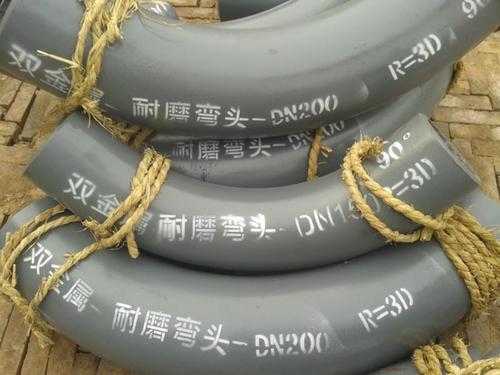
2 試制過程與結果分析
2.1 彎頭材質(zhì)成分選擇
輸送煤粉過程中,彎頭部位承受煤粉的沖擊與 磨損嚴重,因此要求彎頭具備很好的耐磨性,同時, 彎頭的安裝、拆卸、以及使用過程中的維修都要求 其具有良好的焊接性能。 在電廠工況下,高鉻鑄鐵 的抗磨損性能是最好的[1],但脆性很高,若單一使用 高鉻鑄鐵材質(zhì),彎頭不能焊接。使用 16Mn 材質(zhì)鋼管 與之復合鑄造, 不僅使彎頭具備了良好的耐磨性 能,而且實現(xiàn)了焊接,很大程度提升了彎頭的使用 周期。
試 驗 彎 頭 工 作 層 高 鉻 鑄 鐵 各 元 素 含 量 根 據(jù) GB/T8263-2010 中 BTMCr15 選定 w 為:2.0%~3.6% C;≤1.2%Si;2.0%Mn;14%~18%Cr;≤3.0%Mo;≤ 2.5%Ni;Cu≤1.2%;≤0.06%P;≤0.06%S。 彎頭外層 非工作層選用 16Mn 材質(zhì)鋼管。
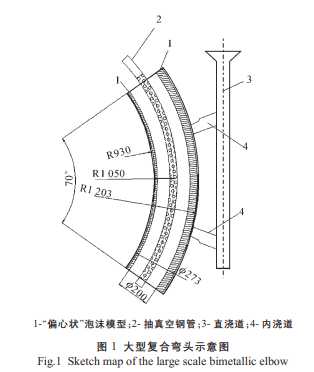
2.2 復合彎頭非工作部位制作工藝
所研 制 的 彎 頭 外 型 尺 寸 如 圖 1,中心 弧 長 為 1 282 mm,對應的半徑為 R1 050 mm,彎頭 兩端所 成中心角為 70°;采購成品 16Mn 材質(zhì)鋼管,鋼管外 徑為 準273 mm,壁厚 6 mm,用線切割的方法,將鋼 管根據(jù)所試制彎頭的角度切分為 7 段, 并按 1∶1 放 大樣進行焊接,形成彎頭的非工作部位。
2.3 工作部位模型制作工藝
工業(yè)發(fā)達國 家在開發(fā)消 失模鑄造工 藝的過程 中,重點對大型鑄件泡沫模型的熱解特性,金屬充 型凝固特性, 干砂充填緊實度等專題進行研究,并 取得了很好效果[3~6]。 因所制彎頭尺寸較大,故內(nèi)部 工作部位采用消失模鑄造工藝制備。
煤粉在輸送過程中,彎頭背部所受的沖擊磨損 最嚴重,所以內(nèi)部工作層設計采用沿弧逐漸加厚的 “偏心”結構,如圖 1 中 1 所示;彎頭內(nèi)部工作層“偏 心”狀模型的制作選用聚苯乙烯泡沫,采用電阻絲 手工切割, 鑄造收縮率為 1%。 將泡沫模型分節(jié)切 割,填充于鋼管彎頭內(nèi),并盡量做到嚴絲合縫,有縫 隙之處用報紙粘貼嚴實,填堵完成后涂刷鎂砂粉涂 料,涂層厚度約 2.0~2.5 mm。 因彎頭尺寸較大,為防 止塌箱,涂料涂刷 4 遍,每層涂刷后在烘干室內(nèi)進 行烘干,待完全干燥后涂刷下一層。
2.4 澆注系統(tǒng)設計
由于彎頭尺寸較大,采用水平式澆注易發(fā)生塌箱事故。經(jīng)試驗,澆注工藝采用如圖 1 中的豎立式階 梯澆注[7]。 階梯澆注系統(tǒng)分 2 層澆道,兩個內(nèi)澆道 向同一方向傾斜;便于補縮、同時防止鐵液冷卻收縮 將其拉裂。 根據(jù)文獻介紹[8],階梯式澆注系統(tǒng)的直 澆道 截面積應大于其他澆道截面積, 研制試驗設 計直澆道截面尺寸 45 mm×45 mm,內(nèi)澆道截面尺寸 30 mm×45 mm,長 180 mm。
2.5 模型合箱
彎頭內(nèi)涂料完全干透后, 將模型與澆注系統(tǒng)組 裝 完整,同時在 彎 頭 內(nèi) 設 置 抽 真 空 鋼 管,圖 1 中 2 所示。 之前試制過程中因沒設抽真空鋼管, 發(fā)生脹箱 和塌箱現(xiàn)象,致鑄件不合格,經(jīng)分析討論其原因為: 彎頭內(nèi)腔型砂緊密度和硬度不夠。 彎頭內(nèi)部設置抽 真空鋼管可增強型砂硬度和緊密度, 有效防止脹箱 等現(xiàn)象發(fā)生。
抽真空鋼管固定于彎頭內(nèi)中心位置, 避免偏心 與內(nèi)壁接觸,防止抽塌。將組裝好的模型整體放入砂 箱內(nèi),檢查涂料有無脫落或“露白”現(xiàn)象,若有發(fā)生及 時用泥粘嚴,避免澆注時型砂進入鑄件形成夾砂。 砂箱內(nèi)以硅砂作為型砂, 模型在砂箱內(nèi)的吃砂 量 為:下 部 90~100 mm,四壁 與 上 部 120~150 mm。 將砂箱置于二維震動臺震動 1 min 左右, 后吊入澆 注坑。 表面覆蓋塑料薄膜,放置澆口杯,將潮砂覆于 薄膜上, 用于固定澆口杯以及防止外濺鐵液燒破薄 膜而泄壓。
2.6 鐵液熔煉與澆注
高 鉻 鑄 鐵 的 熔 煉 在 250 kg 中 頻 感 應 爐 內(nèi) 進 行,按照已設定鐵液的化學成分進行配料計算。 裝 爐時爐料要緊密,以求快速熔化;開始通電 6~8 min 內(nèi)先以小功率送電,待電流沖擊停止 后,逐漸將功 率 增 至 最 大 ; 熔 煉 過 程 中 應 隨 時 推 料 防 止 “搭 橋 ” ,并 陸 續(xù) 添 加 爐 料。 待 爐 料 全 部 熔 化,溫 度 升 至 1 480 ℃時出 鐵 液, 并 開 啟 真 空 泵, 鐵 液 鎮(zhèn) 靜 2~3 min 后進行澆注。澆注完成后將負壓度調(diào)整為 -0.025 MPa,抽真空保持 15 min 關閉真空泵,鑄件 于砂箱內(nèi)保溫 8 h 倒箱。 鑄件在空氣中冷卻。
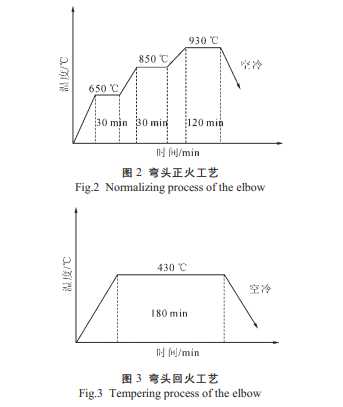
2.7 熱處理工藝
為了提高大型復合彎頭使用壽命, 達到火力發(fā) 電廠輸送煤粉的指標要求, 對彎頭進行了正火和回 火處理。 正火和回火工藝如圖 2 和圖 3 所示。
2.8 耐磨性試驗及結果分析
為對比雙金屬彎頭與單一材質(zhì) 16Mn 彎頭的耐 磨損性能, 分別從研制成功的雙金屬彎頭及 16Mn 彎頭上取樣,進行了磨粒磨損試驗。將 試樣 制 成 50 mm×50 mm×4 mm 的試 樣 塊, 于 NUS-ISO3 型磨粒磨損試驗機上進行磨損試驗, 記 錄 試 樣 減 重 量;對 試 驗 機“往 復 次 數(shù)”及 試 樣 塊 “累計減重量” 用的函數(shù)關系 Origin 軟件進行直線 擬合,分別得到如圖 4 所示的兩條直線,直線斜率 即表示試樣的磨損率。
從圖 4 中直線 斜率可以得 出: 雙 金 屬 彎 頭 試 樣 的 耐 磨 性 能 是 16Mn 材 質(zhì) 彎 頭 耐 磨 性 能 的 2.05倍。
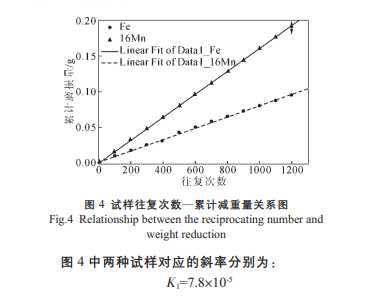
2.9 大型雙金屬彎頭的應用
研制成功的大型復合彎頭在某電廠進行了裝機 試驗,現(xiàn)場跟蹤表明:使用了 18 個月未發(fā)現(xiàn)穿孔失 效現(xiàn)象, 較該電廠原配彎頭使用壽命提高 2~3 倍, 品質(zhì)得到該電廠的認可。
3 結論
(1)采用消失模固液復合鑄造 16Mn 材質(zhì)鋼-高 鉻鑄鐵復合大型彎頭, 既保證了彎頭良好的焊接性 能,同時擁有很高的耐磨性,大幅度增加了彎頭的使 用周期,提高了煤粉輸送效率。
(2)(2)澆注 過 程 中,采 用 豎 立 式 階 梯 澆 注 并 在 復 合 彎頭內(nèi)添加抽真空鋼管,有效解決了塌 箱、脹箱 問題。
(3)(3)與單一材質(zhì) 16Mn 彎頭相比,雙金屬復合彎 頭的耐磨性能是其 2.05 倍, 使用壽命較前者提高 2~3 倍。
- 上一篇:不銹鋼法蘭,彎管精密,鑄造技術
- 下一篇:碳鋼和不銹鋼法蘭連接的腐蝕問題及解決方案