常見問題
高壓三通生產(chǎn)廠家
更新時(shí)間??2021-11-19 07:08 閱讀
管件內(nèi)高壓成形工藝是近幾年發(fā)展起來的一種新的塑性成形技術(shù).本文分析了三通管內(nèi)高壓成形時(shí)的主要變形特點(diǎn)和技術(shù)關(guān)鍵,采用數(shù)值模擬方法給出了不同軸向進(jìn)給速度下零件的壁厚及等效應(yīng)變分布,并分析了軸向進(jìn)給速度對(duì)成形性能的影響.分析結(jié)果表明,當(dāng)軸向進(jìn)給速度過快時(shí),主管中部壁厚增厚嚴(yán)重,形成死皺.當(dāng)軸向進(jìn)給速度過慢時(shí),主管中部容易導(dǎo)致變形區(qū)補(bǔ)料不足而破裂.因此軸向進(jìn)給速度的選取對(duì)內(nèi)高壓成形三通管具有重要影響,對(duì)于成形TP2紫銅三通管,合理的軸向進(jìn)給速度是0.5mm·s-1.
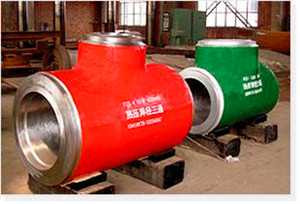
通過對(duì)零件的結(jié)構(gòu)和工藝分析,介紹了在普通車床上采用兩種夾具加工三通接頭的過程和方法,重點(diǎn)分析了兩種車床夾具的設(shè)計(jì)、結(jié)構(gòu)、工作原理、使用方法和注意事項(xiàng)等.經(jīng)驗(yàn)證,該方法能滿足零件的加工要求,夾具結(jié)構(gòu)簡(jiǎn)單、使用方便且安全可靠,既經(jīng)濟(jì)又科學(xué).
以Dynaform板料成形軟件為研究平臺(tái),探索高壓筒體三通口在成型過程中壓邊力、筒體橢圓口的大小及短長(zhǎng)軸半徑比的理想值.根據(jù)數(shù)值模擬分析得到滿足三通口技術(shù)要求的最優(yōu)拉深工藝參數(shù)和模具結(jié)構(gòu)參數(shù)組合為:壓邊力380 kN,虛擬沖壓速度1000 mm/s(相當(dāng)于實(shí)際沖壓速度的10倍),凸凹膜間隙0.85 mm,短長(zhǎng)軸半徑比0.7.該結(jié)果可以為模具設(shè)計(jì)提供參考.
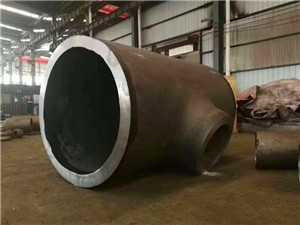
為探討5083鋁合金等徑正三通的內(nèi)高壓成形規(guī)律,采用有限元模擬首先分析了成形過程的變形情況,其次研究了壁厚以及應(yīng)力、應(yīng)變的分布,用成形時(shí)應(yīng)力、應(yīng)變的變化解釋了形成厚度分布趨勢(shì)的原因.模擬結(jié)果表明,支管頂部壁厚減薄,主管以及與沖頭接觸處明顯增厚.在內(nèi)高壓成形的三通鋁合金管在幾何尺寸及壁厚分布方面,實(shí)驗(yàn)結(jié)果與有限元模擬值基本吻合.
為了解Y型三通管內(nèi)高壓成形時(shí)的壁厚分布及成形壓力對(duì)壁厚的影響規(guī)律,通過數(shù)值模擬和實(shí)驗(yàn)對(duì)Y型三通管的內(nèi)高壓成形過程進(jìn)行了研究,分析了3個(gè)不同成形階段零件的壁厚分布規(guī)律和成形過程中零件典型點(diǎn)壁厚隨內(nèi)壓的變化規(guī)律.研究表明,成形后零件左側(cè)過渡區(qū)圓角處壁厚最大,右側(cè)過渡區(qū)圓角處次之,枝管頂部壁厚最薄.利用數(shù)值模擬,研究了不同終成形壓力對(duì)零件壁厚分布的影響,研究發(fā)現(xiàn)隨著終成形壓力的提高,零件的最大增厚率變化不明顯,但零件的最大減薄率有顯著的增加.
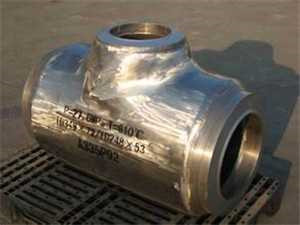
對(duì)于Y型三通管,由于其結(jié)構(gòu)的不對(duì)稱性,內(nèi)高壓成形過程中左右沖頭的軸向補(bǔ)料比對(duì)成形有較大的影響.通過實(shí)驗(yàn)和數(shù)值模擬,研究了補(bǔ)料比對(duì)Y型三通管的壁厚影響規(guī)律以及成形中產(chǎn)生的缺陷.結(jié)果表明:成形后零件左側(cè)過渡區(qū)圓角處壁厚最大,右側(cè)過渡區(qū)圓角處次之,枝管頂部壁厚最薄;增加補(bǔ)料比能在一定程度上改善枝管部分的壁厚減薄,但過度加大左右補(bǔ)料比,會(huì)使試件左側(cè)圓角處產(chǎn)生內(nèi)凹缺陷.
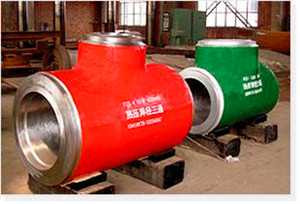
通過對(duì)零件的結(jié)構(gòu)和工藝分析,介紹了在普通車床上采用兩種夾具加工三通接頭的過程和方法,重點(diǎn)分析了兩種車床夾具的設(shè)計(jì)、結(jié)構(gòu)、工作原理、使用方法和注意事項(xiàng)等.經(jīng)驗(yàn)證,該方法能滿足零件的加工要求,夾具結(jié)構(gòu)簡(jiǎn)單、使用方便且安全可靠,既經(jīng)濟(jì)又科學(xué).
以Dynaform板料成形軟件為研究平臺(tái),探索高壓筒體三通口在成型過程中壓邊力、筒體橢圓口的大小及短長(zhǎng)軸半徑比的理想值.根據(jù)數(shù)值模擬分析得到滿足三通口技術(shù)要求的最優(yōu)拉深工藝參數(shù)和模具結(jié)構(gòu)參數(shù)組合為:壓邊力380 kN,虛擬沖壓速度1000 mm/s(相當(dāng)于實(shí)際沖壓速度的10倍),凸凹膜間隙0.85 mm,短長(zhǎng)軸半徑比0.7.該結(jié)果可以為模具設(shè)計(jì)提供參考.
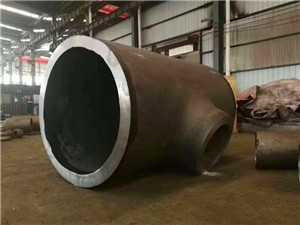
為探討5083鋁合金等徑正三通的內(nèi)高壓成形規(guī)律,采用有限元模擬首先分析了成形過程的變形情況,其次研究了壁厚以及應(yīng)力、應(yīng)變的分布,用成形時(shí)應(yīng)力、應(yīng)變的變化解釋了形成厚度分布趨勢(shì)的原因.模擬結(jié)果表明,支管頂部壁厚減薄,主管以及與沖頭接觸處明顯增厚.在內(nèi)高壓成形的三通鋁合金管在幾何尺寸及壁厚分布方面,實(shí)驗(yàn)結(jié)果與有限元模擬值基本吻合.
為了解Y型三通管內(nèi)高壓成形時(shí)的壁厚分布及成形壓力對(duì)壁厚的影響規(guī)律,通過數(shù)值模擬和實(shí)驗(yàn)對(duì)Y型三通管的內(nèi)高壓成形過程進(jìn)行了研究,分析了3個(gè)不同成形階段零件的壁厚分布規(guī)律和成形過程中零件典型點(diǎn)壁厚隨內(nèi)壓的變化規(guī)律.研究表明,成形后零件左側(cè)過渡區(qū)圓角處壁厚最大,右側(cè)過渡區(qū)圓角處次之,枝管頂部壁厚最薄.利用數(shù)值模擬,研究了不同終成形壓力對(duì)零件壁厚分布的影響,研究發(fā)現(xiàn)隨著終成形壓力的提高,零件的最大增厚率變化不明顯,但零件的最大減薄率有顯著的增加.
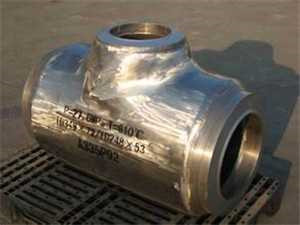
對(duì)于Y型三通管,由于其結(jié)構(gòu)的不對(duì)稱性,內(nèi)高壓成形過程中左右沖頭的軸向補(bǔ)料比對(duì)成形有較大的影響.通過實(shí)驗(yàn)和數(shù)值模擬,研究了補(bǔ)料比對(duì)Y型三通管的壁厚影響規(guī)律以及成形中產(chǎn)生的缺陷.結(jié)果表明:成形后零件左側(cè)過渡區(qū)圓角處壁厚最大,右側(cè)過渡區(qū)圓角處次之,枝管頂部壁厚最薄;增加補(bǔ)料比能在一定程度上改善枝管部分的壁厚減薄,但過度加大左右補(bǔ)料比,會(huì)使試件左側(cè)圓角處產(chǎn)生內(nèi)凹缺陷.
- 上一篇:Y型三通生產(chǎn)廠家
- 下一篇:高壓管件生產(chǎn)廠家